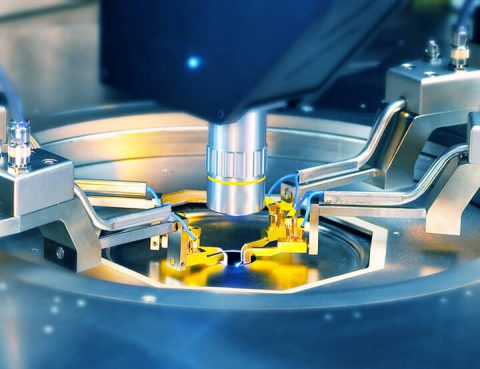
August 17, 2023
Parametric measurements in the DC domain wield significant influence across all stages of semiconductor product development and production, spanning diverse device categories and semiconductor technologies.
August 17, 2023
Parametric measurements in the DC domain wield significant influence across all stages of semiconductor product development and production, spanning diverse device categories and semiconductor technologies.
Parametric measurements in the DC domain wield significant influence across all stages of semiconductor product development and production, spanning diverse device categories and semiconductor technologies. Their significance extends to advanced materials exploration, process understanding, device analysis and simulation, design issue identification, process vigilance, and wafer sorting during manufacturing.
The precision and consistency achieved through accurate DC parametric measurements encompassing IV, CV, pulsed, and high-power assessments lead to a reduction in uncertainties. The credibility of the outcomes expedites device validation and engenders more refined models and design resources. Consequently, designers are empowered to expedite the release of more competitive products to the market.
Our innovation has reshaped the landscape of analytical probe systems, tailored precisely for this purpose – cultivating an electrically untainted environment for on-wafer measurements. By nullifying the impact of external factors that might negatively impact test outcomes, the probing apparatus effectively melds into the background, rendering itself “invisible” to the measurement apparatus. Since the advent of the inaugural MicroChamber® probe station in 1991, FormFactor’s have consistently been driven by the same mission – facilitating customers’ success through the strategic deployment of optimal data for informed decision-making.
Challenges to Measurement Integrity
Numerous elements have the potential to compromise DC electrical measurements. External factors, such as electromagnetic interference and radio frequency disturbances emanating from sources like cellular networks, radio/TV towers, nearby electronics, and equipment, in addition to physical variables like temperature and vibration, can introduce electrical noise into the data.
Internal components of the measurement system also wield influence on outcomes. For instance, poorly constructed signal paths can result in current leakage, resistive or thermal voltage shifts, materials’ energy retention, and electrical noise originating from critical probe system elements like power supplies, stage motors, thermal systems, and computers.
When not appropriately managed, these factors can substantially erode electrical precision, leading to data discrepancies and a wider distribution of results within the sample set. The repercussions of inaccurate data are far-reaching and costly, encompassing the need for retesting, extended modeling cycles, postponed product launches, and the devaluation or underperformance of products.
Unmatched Experience
FormFactor’s seasoned design team has consistently elevated the standard of excellence in electrical measurements. Through a series of innovative breakthroughs, crafted in close collaboration with our esteemed customers, we have crafted an extensive line of remarkably potent technologies. These include but are not limited to:
These technologies have demonstrated their prowess across a broad spectrum of temperatures and in fully automated scenarios, where challenges grow exponentially.
This unwavering commitment to safeguarding the integrity of electrical measurements is a hallmark that distinguishes a FormFactor analytical probe system, enabling customer success through uncompromised data reliability.