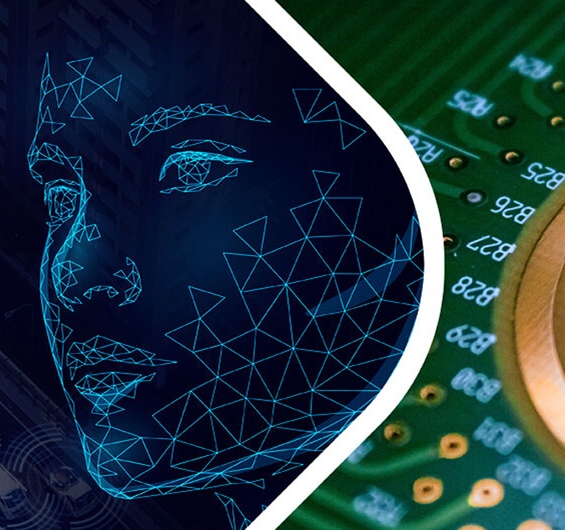
July 12, 2024
FormFactor meets these challenges with a variety of specialized manual, semi-automated, and fully automated probe stations designed for high-precision single and dual-sided optical measurements on wafers.
July 12, 2024
FormFactor meets these challenges with a variety of specialized manual, semi-automated, and fully automated probe stations designed for high-precision single and dual-sided optical measurements on wafers.
Vertical Cavity Surface Emitting Lasers (VCSELs) are an emerging technology with diverse applications in infrared lighting, proximity sensors, high-resolution video displays, atomic clocks, and facial recognition systems. These semiconductor lasers emit light perpendicular to the chip surface and are constructed using a complex multilayer structure, typically applied to the substrate through molecular beam epitaxy (MBE) or metal-organic chemical vapor deposition (MOCVD).
The epitaxial layers include an active layer responsible for photon generation, trapped between two Bragg reflectors (DBRs) that function as mirrors. These reflectors bounce the light back and forth through the active layer, enhancing amplification. Generally, VCSELs produce an output power ranging from 0.5 to 5 mW, with common emission wavelengths between 750 and 980 nm, enabled by a GaAs/AlGaAs material system.
New applications for VCSELs in smartphones and the automotive industry are propelling the VCSEL market to unprecedented levels. In smartphones, 3D sensing for facial recognition is a pivotal application, with some devices incorporating up to three VCSEL dies. Meanwhile, emerging automotive uses, such as driver monitoring, infotainment control, and LiDAR, are also expected to significantly drive market expansion and support sustained growth.
As 3D sensing technology powered by VCSELs continues to discover new applications, the technology we regularly rely on will become more secure, safer, and smarter.
Challenges to Consider with VCSEL Probing
Testing VCSEL devices on wafers presents multiple challenges. One significant requirement is the ability to perform single and dual-sided testing, which involves probing from either the front or backside of the wafer. The probe system must accommodate thin, warped wafers (such as GaAs, InP, and others in 4” and 6” sizes). Due to the impossibility of using a thermal chuck for both-sided probing, the measurement setup necessitates a localized cooling/heating source to ensure accurate cool-to-hot dual-sided testing.
Furthermore, executing a complex test suite that includes measurements such as far-field, near-field, and light-I-V (LIV) demands multiple optics and detectors, necessitating several test setups and passes to complete these measurements. Multi-sided testing also adds complexity to both the probe card design and the device under test (DUT) temperature control.
MicroLED Display Technology
MicroLED (μLED) display technology is garnering significant attention, and μLED displays are poised to debut in consumer products shortly. Emerging applications for μLED displays span a range of sectors, including wearables, smartphones/tablets, TVs, virtual/augmented reality (VR/AR), and automotive.
Compared to OLED, LCD, and other display technologies, μLED displays offer higher resolution, greater dynamic range, faster response times, and lower power consumption, which translates to longer battery life.
Challenges to Consider with MicroLED Probing
A key requirement for on-wafer MicroLED testing is the capability for single and dual-sided testing. This involves probing on one side while conducting optical measurements with an integrating sphere and detector on the other side. The probe system must be capable of handling thin, warped wafers (such as GaAs, InP, and others, in 4” and 6” sizes) and ensure precise probe-to-pad alignment on very small pad/bump sizes and pitches.
Additionally, the system must facilitate efficient, high-speed production-style testing of millions of devices under test (DUTs) per wafer, featuring high parallelism and rapid, accurate stepping.
Delivering Technology for VCSEL and MicroLED Testing
Testing optical devices directly on a wafer demands advanced automated probing solutions. FormFactor meets these challenges with a variety of specialized manual, semi-automated, and fully automated probe stations designed for high-precision single and dual-sided optical measurements on wafers.
For more information on these VCSEL and MicroLED testing technologies, visit the VCSEL and MicroLED Application page on our website, or download the VCSEL System Data Sheet.